6 Things You Need to Know About Backorders
We take fulfillment personally.
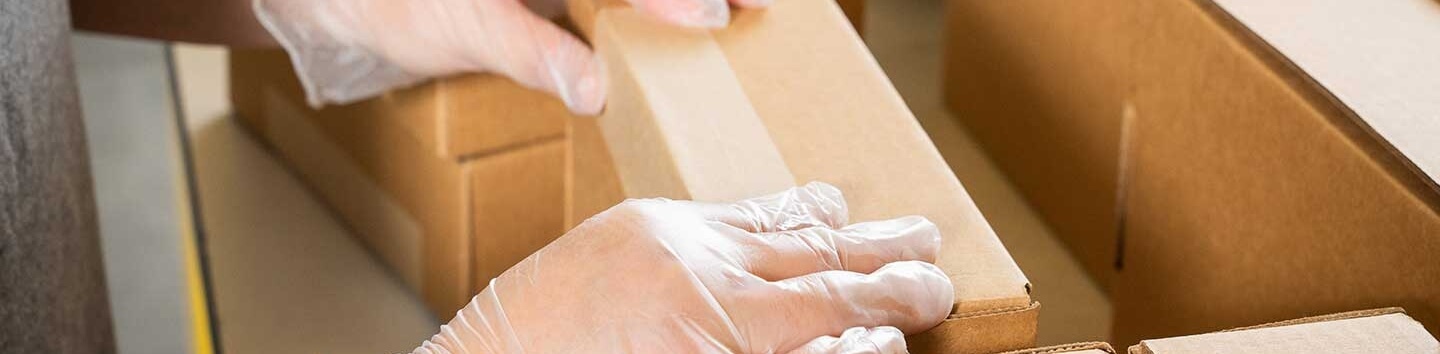
6 Things You Need to Know About Backorders
When you sell something everyone wants, sadly, backorders are frequently a seemingly unavoidable problem. No product can be manufactured in limitless amounts. When demand exceeds supply, backorders are typically the result. Due to backorders, products becoming unavailable can even be a problem for companies that are longstanding and those that have a good reputation. But they may be more preventable by partnering with a reliable 3PL.
What Causes Backorders?
When a product is currently out of stock, a backorder occurs because supply couldn’t keep up with demand. Once inventory is replenished, backorders become available again. Any number of influences go into determining just when that occurs. While an order may be completed by customers, a backorder stops them from receiving their product for an extended period of time. This could cause customer dissatisfaction and serious frustration. The following factors may be the cause of backorders:
- Manufacturer issues: A manufacturer losing access to the raw materials needed to make a product could result in backorders. Manmade or natural disasters such as conflict on an international level could prevent raw materials access needed for merchandise production.
- Extremely high demand: Popular products will always be in high demand, and most businesses plan for it. But, if capacity to provide is exceeded by demand, backorders often occur.
- Insufficient safety stock: Kept on hand for supply chain failures or emergencies, safety stock consists of excess products. If this safety stock is not adequately prepared or counted, because of insufficient stock, customers might still experience backorders. Make sure you have safety stock!
Is Your Supply Chain Broken?
Sooner or later, most businesses that supply a product – as opposed to a service – experience the “supply-chain blues”. As you’ve already read, there can be any number of circumstances that can lead to problems within a supply chain, resulting in backorders and “out of stock” issues.
As an example, numerous barges were tied up as a result of COVID-19. All of the products on the barges were needed by businesses for one purpose or another – from a piece being an integral part of their operation or simply to fulfill orders already placed by consumers (and everything in between). Fortunately, the problem is finally getting resolved, slowly but surely.
But rather than being a cause, was COVID-19 merely a disruptive trigger? The causes of supply chain issues, though many, can be associated with several standard classes of instigators just waiting for a trigger, including: Sub optimization, overconcentration in markets, and poorly executed supply chain management. Let’s look at each of these.
Sub Optimization
Rather than directing all company parts toward the achievement of shared success measures and common goals, in sub optimization, departmental goals are solely focused on. Rather than concentrating on ways for a company to succeed as a whole, the success of a single division or department is concentrated on instead. A company is made up of many parts – all of which must work together. Concentrating on only one department, while ignoring others, is a recipe for disaster and can end up causing supply chain issues.
Overconcentration in Markets
In several ways, approaches by corporations are out of sync:
- When markets depend on only one or a couple of factories as suppliers, should disaster strike those factories, the materials needed by those depending on them will cease until the problem can be resolved.
- To gain improved terms and importance, the number of vendors is sometimes reduced by companies as they seek to simplify vendor management and become bigger businesses.
- In various industries, the number of potential vendors is reduced due to consolidation among companies.
Poorly Executed Supply Chain Management
For decades, popular strategies like “just-in-time” or “lean” supply chains have been used. This reduces the amount of in-transit and on-hand inventory through greater production and distribution efficiency. In other areas of a business, investments can be made with the freed-up money. Unfortunately, while these tools may be beneficial in some ways, the approach that a business uses to implement them can have detrimental effects on the supply chain and order fulfillment. Should some type of problem or disaster strike, these companies will simply be ill-prepared.
By partnering with a reliable 3PL service, your supply chain worries can be lessened considerably.
How to Prevent or Reduce Backorders
Don’t ignore the risk of products being backordered! In addition to revenue loss for your business, backorders can end up being responsible for loss of goodwill and threaten the reputation of virtually any company. Here are a few ways to avoid or decrease backorders: Do all you can to place orders early and often!
- Calculate and Install reorder points
Your reorder point involves the minimum amount of stock keeping units – or SKU – that the company must have available prior to reordering additional products from a manufacturer. The point formula for reorder can be determined by adding up the lead time demand as well as the daily safety stock. Custom-made technology is employed by certain providers that make it easier to create and calculate reorder points. Service providers such as these will also alert you when it is time to order more inventory. This way you’ll be more likely to dodge stressful order pileups, not be able to fulfill those orders and other associated scenarios. Make things easier, for your customers and yourself, by enlisting some professional assistance courtesy of a highly rated 3PL provider like Alpaka.
- Use multiple suppliers
Relying on just one supplier is challenging, particularly if they’re in locations prone to natural disasters or political issues. Have more than one source as a backup in the event that a problem arises with your usual supplier. Expect the seemingly unexpected! Consider holding a ‘trend’ meeting.
- Establish safety stock
Ecommerce businesses in particular should set up an inventory management system to monitor stock of products in real time. In this manner, you’ll be able to predict increases in demand better and build a safety stock large enough to cover them. Review, look at trends and walk the floor.
Constantly keep an eye on products that are the most popular and acquire sufficient quantities of safety stock. This way, to satisfy your customers, you will always have enough products on hand, and you can keep your revenue flow steady. Make sure to review! Talk to your team. Check in on stock. Notice trends.
Or… rely on Alpaka as your new logistics partner. You’ll finally be able to put your mind at ease.
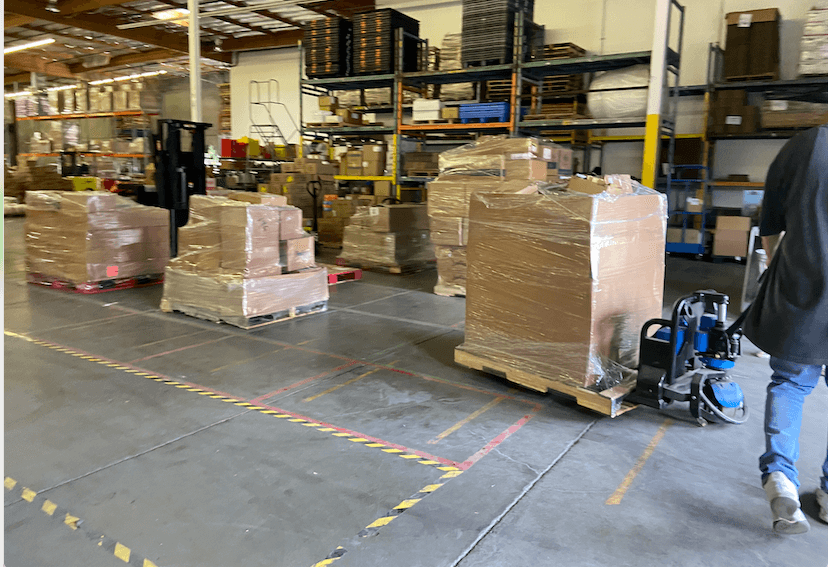